Worklog: Tetris Shelves – Planning, Materials, and Tools
Will wanted to build a set of shelves shaped like Tetris blocks for his daughter's room. This is his first work log documenting the process.
From the very first time I saw someone’s worklog on the Internet, I’ve always wanted a set of Tetris shelves. Tetris shelves are modular shelves, shaped like the standard Tetris pieces, that you can stack in configurations you’d find in the game. Unfortunately, pre-made shelves are expensive, so I’ve never been able to justify spending the money or taking the time to actually build a set. At least, I couldn’t until I had a nursery to decorate.
That’s right, I’m building Tetris shelves for my daughter’s nursery. Before you ask, yes, I know that they’re nerdy. Yes, I know they aren’t practical. Yes, those shapes are going to be pretty tricky to make. No, I don’t have much experience with woodworking. I’ve built some quick-and-dirty shelves before, but I’ve never done any kind of fine carpentry work.
I’m happy to share my plans, as well as the CAD files I created, and I’ve recorded video of much of the build process for a series of posts about the shelves. But, this isn’t a guide that explains the proper way to build a set of Tetris shelves. I’m absolutely positive that I made lots of mistakes as I was building–most were likely harmless, but I did a couple of things that were actually dangerous. I’m just learning the basics of cabinetry and furniture building as I go, so I’m not in a position to teach even the most basic stuff. I’d love feedback from people who have more experience, as well!
This is intended to show you my process as I went about learning a new skill, or set of skills in this case. I did a ton of research, drew diagrams, built CAD files, watched videos on the Internet, and talked to friends, experts, retailers, and even people on Twitter to get advice. Unless something goes horribly wrong as I assemble the last few shelves and finish them, this will likely be a three-part story: Planning, Assembly, and Finishing.
I started on this project without knowing anything. I didn’t know what type of wood to use–whether to use hardwood, a rough composite plywood, a finer plywood, or something weird that I didn’t even know existed. I didn’t know how big I could make them, how deep they could be, or anything about finishing them. Before I started on this, I knew how to work a handful of hand power tools–circular saws, reciprocal saws, and the like–but hadn’t ever really used stationary shop saws, like a table saw or miter saw.
My first step was to figure out the design and pieces I’d need to assemble shelves that look good and can hold a reasonable amount of stuff. In the game, there are seven basic Tetris pieces, called Tetrominos. However, two of the pieces are mirror images of each other, so for the purposes of my design, I only had to figure out how to make five pieces. I sketched each piece, then calculated dimensions at a couple of different scales. After looking at the things we want to put on the shelves–kids’ books, toys, lamps and pictures–I chose an initial scale for the shelves of 12 inches per block.
Sketching this kind of project is why I love grid-lined notebooks like the Field Notes notebooks–they make it easy to make to-scale drawings. I drew multiple ways to connect each joint in the shelves, then selected the ones that seemed to apply stress most evenly in the configurations I thought I’d use.
After I worked out the measurements, I loaded up 123D Design to convert my sketches into 3D models. 123D Design is a stripped down, free CAD software from AutoDesk. 123D Design lets you start your work as a 2D sketch, then extrude it to make it three dimensional. While this wouldn’t work well for more complex models, it was perfect for a set of shelves.
After I built 3D models of each piece, I tried to assemble them in 123D Design, but the software isn’t really designed for that and I wasn’t able to get anything aligned properly. However, because we have access to a 3D printer, I was able to run off scale models of the pieces to see how the shelves would fit together in the real world. If you don’t have access to a 3D printer, you could do the same thing by assembling a model from foamcore, cardboard, or even just cutting paper sketches of your design out.
When I was using the scale models, I realized I’d made a mistake in a couple of the more complex pieces. It wasn’t something that showed up in the CAD assembly, but it was immediately obvious when I tried joining the S and Z pieces to a T. A couple of quick CAD file changes followed by an hour or so of printing, and I was back in business with a design that I was confident would work–if I could assemble it properly.
The scale models also let me physically see different possible configurations for the shelves. Since different Tetrominos require different size sides, once I started cutting my materials, I’d be locked into using those pieces. Once I found a configuration of pieces I liked, I made sure they’d fit in the baby’s room. Finally, I checked out other shelves pretty much everywhere I went to figure out the optimal depth of the shelves. I ended up building 10-inch deep shelves and made each cube of the Tetromino 11 inches.
Materials
Next up was figuring out the right kind of wood to use for the shelves. While I appreciate Jamie’s love of welded square-tube steel, it doesn’t seem appropriate for a kid’s room. Wooden shelves seemed like the smart choice, but I was worried about both warping and the expense if I used solid hardwood, but I was also worried that plywood wouldn’t be sturdy enough to join at the corners. Adam suggested I look at thin-ply plywood, which contains many more layers than typical plywood–13 layers instead of 7 or 8. This makes it both more rigid and less likely to warp for the type of project I’m working on.
Next, I visited the local hardwood store (MacBeath Hardwood in San Francisco, but you’ll likely have something similar in the lumber or cabinetry section of your local Yellow Pages) to see what was available. If you’ve never been to a shop that specializes in lumber for furniture and cabinetry, it’s dramatically different than the lumber aisle in your local Lowes or Home Depot. MacBeath stocks dozens of different species of wood, suitable for any project. At the shop, I asked about the thin-ply and we discussed my project, to make sure it was a good fit. After we looked at a few different types of wood, I ended up going with a 3/4-inch thick, formaldehyde-free, birch thin-ply that was made in the Pacific Northwest. The plywood comes in 4-foot by 8-foot sheets and costs about $110/sheet. By default, the sheets are too big to fit in my car, but the guys at MacBeath said they’d be happy to do a couple of quick cuts so my wood would fit in the car.
Before I was able to buy the plywood and cart it home, I had to figure out what size pieces I needed, and what the optimal way to carve those sizes out of two 4’x8′ sheets of plywood was. After a lot more sketching, I realized that simply cutting each sheet of the plywood into two 4’x4′ sheets would leave me plenty of room to work and minimize my waste. Your project may be different, so if you can’t haul an uncut sheet of plywood, make sure you know where your cuts should be before you go to buy materials. I later learned that I could have paid an outside contractor to pre-cut the sheets to my specifications, which would have been much easier, cost just a bit more than the tool rental, and saved me a day of fairly difficult work. Lessons learned.
The rest of the materials were simpler. After talking to several woodworkers and investigating my options for assembling the shelves on the Internet, I decided use biscuits instead of one of the more advanced joints. While I understand they aren’t the strongest possible option, they seemed like a good balance between joint strength and my rudimentary carpentry skills.
Biscuit joints require that you cut a slot in each piece of wood to be joined. The slots align with each other, and you fill them with wood glue and a wooden biscuit. The biscuit helps you line up the joint and also absorbs moisture from the glue, which causes the biscuit to swell and helps strengthen the connection. The good news is that both the biscuits and the glue are relatively inexpensive–a tub of 100 #20 biscuits (the large ones) cost about $5 and a gallon of Tightbond III wood glue was $30 from Amazon.
To finish the shelves, I am priming and painting them with water-based latex paints and primers. After I get the final coats of paint on (and sanded to my liking), I’ll either add a couple of coats of polyurethane or use furniture wax to seal and protect the shelves.
Now, I have a plan to build my shelves, I know what materials I need, and I just need to round up the tools.
Tools
Going in, I knew I needed a way to precisely make long cuts that split the plywood sheets into 10-inch boards and cut those resulting boards to a perfectly square 90 degrees at exactly the right point. My reading suggested that a table saw was the right tool to make the long rips, while a miter saw would be better to make the precise 90-degree cuts required for the ends. I shopped around to price out entry level tools, and quickly realized that I didn’t want to spend $500 to $1,000 just on tools.
Then I looked at renting shop space for a day to do the rips and cuts. Unfortunately, that wasn’t practical without a good way to haul the wood. After the plywood was cut, I had just under 90 board-feet of wood to tote around, which seemed like a bad idea.
After consulting the Yellow Pages and talking to some folks at equipment rental places, I found a place that rents power tools by the day: Action Rentals. For a single day, I was able to rent a 12-inch sliding, compound miter saw and a 10-inch table saw for about $60. While that meant I needed to get all of my cutting done in a single 24-hour period, it was doable, with good planning. While both saws were well maintained, neither saw’s blades were exactly right for what I wanted to do. I ended up visiting Lowes and bought a couple of new blades more in line with my project. I only ended up using one (I returned the other), but I didn’t want to ruin $200 worth of lumber because I didn’t have the right blade for a rental saw.
While I’m sure there are multiple other ways to cut the holes for biscuits, I was able to borrow a plate joiner to simplify the task. A plate joiner is a specialized saw with guides that make it difficult to mess up your cuts and a plunging saw blade that cuts a slot that’s the appropriate shape for standard sized biscuits. Typically they run $180-$200, so borrowing one saved me a ton of money.
As frequently gets you in this kind of project, the assorted other stuff adds up. Luckily, I already had an orbital sander and ShopVac, both of which will be massive time savers. I have a circular saw to do rough cuts when I’m breaking down the big pieces of plywood, and I have plenty of brushes and painting supplies. I already had a respirator to use while sanding and safety glasses, to wear pretty much all the time.
What I didn’t have, were clamps. At first, I thought I could make do with a handful of corner clamps and a C-clamp or two, enough to do two or three joints at a time. It quickly became clear that I needed to clamp both sides of every single joint on a piece simultaneously, and the pieces needed to be clamped in place for at least 12 hours each. That meant I needed 16 corner clamps, unless I wanted each piece to take multiple days. Even at $7 each for the cheap clamps, clamp costs added up quickly. I’m sure I’ll use them for something else in the future, but Spending $150 on clamps was kind of a bummer.
So there we are. At this point in the process, I have plans, materials, and tools. I’ve spent about $270 in materials, $150 on clamps, and $60 on tool rental, but more importantly, I’ve spent 30 hours sketching, making CAD models, and printing scale models and another 10 or so watching instructional videos and reading about techniques and materials. Now it’s time to put what I’ve learned to the test and start cutting, gluing, clamping, and sanding. Next week, we’ll talk about actually breaking down the plywood, cutting biscuit slots, gluing the shelves together, and figuring out the right way to clamp corners. In the meantime, I’d better get back to my sanding.
Part 2 of the Tetris Shelves Worklog is up. There’s video and even an animated GIF
13 thoughts on “Worklog: Tetris Shelves – Planning, Materials, and Tools”
Leave a Reply
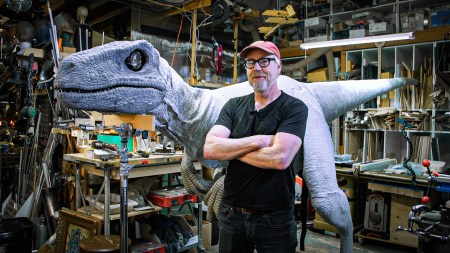
One Day Builds
Adam Savage’s One Day Builds: Life-Size Velocirapt…
Adam embarks on one of his most ambitious builds yet: fulfil…
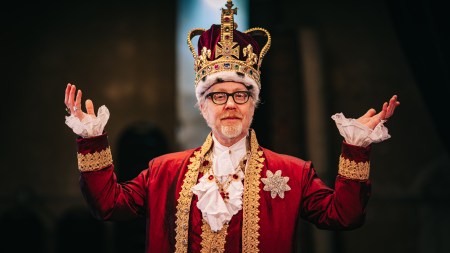
Show And Tell
Adam Savage’s King George Costume!
Adam recently completed a build of the royal St. Edwards cro…
All Eyes On Perserverance – This is Only a Test 58…
We get excited for the Perserverance rover Mars landing happening later today in this week's episode. Jeremy finally watches In and Of Itself, we get hyped for The Last of Us casting, and try to deciper the new Chevy Bolt announcements. Plus, Kishore gets a Pelaton and we wrack our brains around reverse engineering the source code to GTA …
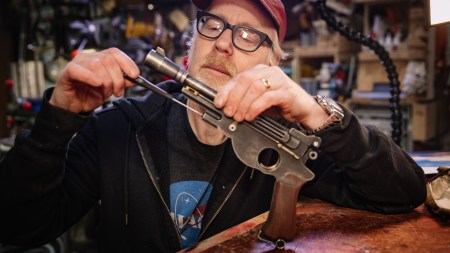
One Day Builds
Mandalorian Blaster Prop Replica Kit Assembly!
Adam and Norm assemble a beautifully machined replica prop k…
House of MCU – This is Only a Test 586 – 2/11/21
The gang gets together to recap their favorite bits from this past weekend's Superb Owl, including the new camera tech used for the broadcast and the best chicken wing recipes. Kishore shares tips for streamlining your streaming services, and Will guests this week to dive into the mind-bending implications of the latest WandaVision episod…
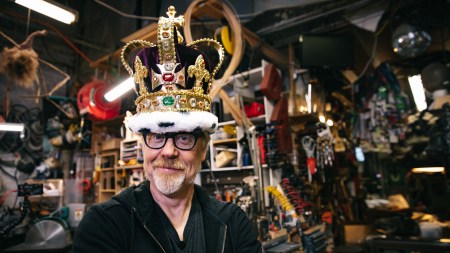
One Day Builds
Adam Savage’s One Day Builds: Royal Crown of Engla…
One of the ways Adam has been getting through lockdown has b…
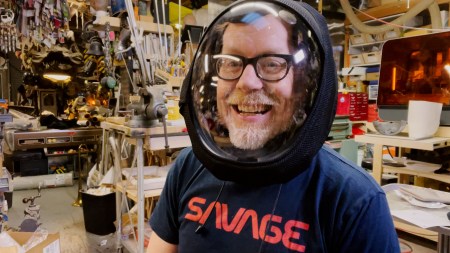
Making
Adam Savage Tests the AIR Active Filtration Helmet…
Adam unboxes and performs a quick test of this novel new hel…
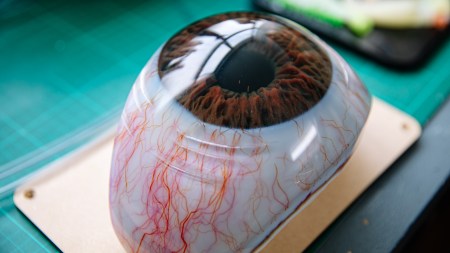
Making
Weta Workshop’s 3D-Printed Giant Eyeballs!
When Adam visited Weta Workshop early last year, he stopped …
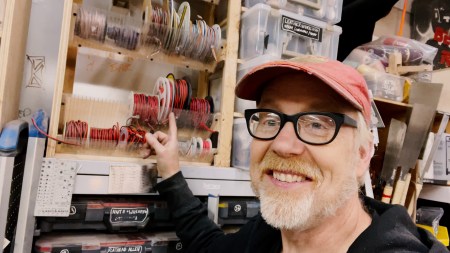
One Day Builds
Adam Savage’s One Day Builds: Wire Storage Solutio…
Adam tackles a shop shelf build that he's been putting off f…

Show And Tell
Mechanical Dragonfly Automata Kit Build and Review
Time for a model kit build! This steampunk-inspired mechanic…
That’s expensive ply-wood!! Did you choose that wood mainly for strength in joining the corners?
I disagree with the practicality of these shelves; with all the junk kids accumulate the versatility of these shelves will quickly manifest their value.
That is awesome Will! I wish I had more time to make projects like these!
Why use the wood glue and biscuits instead of nails? Do professional furniture makers sort of snub their noses at nails?
Also, it looks awesome!
You really should use biscuits and join the corners properly for shelving, so you don’t have exposed nails.
I prefer to use a table saw for all the necessary cuts in most cases, even 90* miter cuts just using a sled. Something to keep in mind for next time if tool rentals cost more for both instead of just one!
Hahaha, whenever I was moving in/out somewhere I always would ask my friends “Now who’s the best at Tetris?”
Don’t you know a couple of guys who already have a serious shop? Why did you not consider asking Adam to use some of his tools for a day, or was it not possible for some reason?
Makes sense! I’m used to using a pretty large(36″ travel for the fence alone, plus the other side of the table), very heavy Iron top table saw. We’ve run full sheets though but its a bit awkward and you need a lot of floor space to accomplish it. Mainly when making custom arcade sticks we never even used a chop saw, as we were buying all the tools and found a good quality tablesaw to be more than adequate with a proper home-made sled for virtually any cut we needed, and it made cleaner cuts than a borrowed chop saw we tried out! Probably depends more on the type of Table Saw you’re using too, as a smaller contractors portable table saw would be difficult to use.
You’ve got to consider that if Will was planning on doing a bit of a guide for us readers, information and experiences on/from equipment rental is more valuable for beginners than “borrow your shop-owner-friends’ tools” 😉
Personally, I totally agree with Will. Borrowing tools from friends isn’t that fun, even more so when your a beginner-level user of them. I’d rather rent, because then I know the owner expects a ding or two when getting them back. 🙂
Haha, I understand.
When it comes to a new process, I just feel more comfortable working with my own tools, or on rented equipment. That way, once I learn to work through the process I can buy nicer tools and know exactly what I need or don’t need. The cash I’ve saved on Techshop classes and tool access is nothing short of amazing.
Any reason why you didn’t opt for making the tetris-shelves at Techshop, seeing as how you’ve talked about taking classes there? If it was only a problem transporting materials (which as a non-driver I know very well), I believe they let you order materials and have them delivered there, and I believe you can rent storage for large sheets of material.
Cool project. Interested how it will look once everything is complete.
Impressive so far. You’ve managed to think your way through a few of the common points people make mistakes. Given I live out in the sticks, I have room and chances to mess up, but so far I’m quite impressed. As for the clamps… yeah, you will never have enough. It may seem like a cop-out but later on you may want to put a few brackets on the corners, just in case.
Are using anything to join the corners other than the biscuits? All the weight placed on that shelf needs to be carried in the joint, which has me a little worried.
I did a quick simulation on it just to illustrate it, 40lbs on the top surface, bottom surface fixed, and this is a solid part (so no joints, not great assumptions but good enough for starters):
You can see the highest stresses near the corner. From the properties of a general plywood you can find here:http://www.matweb.com/search/DataSheet.aspx?MatGUID=bd6620450973496ea2578c283e9fb807
As long as the biscuits aren’t concentrating the stress you should be fine, even if someone goes climbing on it. I would need to look more into it to say that for sure though.
No better excuse for finding a new project than having spent a pile of money on equipment… *stares at twice-used sandblasting equipment* =)