Maker Profile: John Whitmarsh’s Mixed Media Sculptures
What happens when you put traditional artists in a high-tech workshop with access to the latest in CNC equipment? That's one of the goals of Autodesk's Artist in Residence program, and this week, we're profiling a few of the makers given free rein in this awesome workspace.
Sitting amongst the chocolate shops, posh restaurants, America’s Cup hangars, and other touristy attractions of San Francisco’s Embarcadero district lies Autodesk’s Pier 9 workshop—an office space filled with 3D printers, CNC routers, a woodshop, metal shop, and even a test kitchen. But you might wonder: why would Autodesk—a software company—assemble a mountain of high-tech hardware that dwarfs any private man cave and rivals public membership-based workspaces such as TechShop? The short answer is that since the majority of the equipment in the space runs on Autodesk software, having said equipment close at hand lets software developers stay abreast of the newest, coolest ways its digital tools are being used. To that end, the company created an Artist In Residence program to put those machines to good use.

Open to anyone 18 or older, Autodesk’s AIR program aims to put these cutting-edge tools into creative hands and, essentially, let them run free. Artists accepted to the program are granted unrestricted access to the Autodesk facilities, giving them the chance (as well as the training) to use the kind of top-level production equipment they might never otherwise be able to access. Sculptors who’ve previously worked with clay, for example, can experiment with a paper 3D printer. Collage artists can tinker with the latest 3D scanners. The idea is to let loose Picasso in Tony Stark’s lab. In return, the artists deliver at least one Instructable guide (also owned by Autodesk) for a project they worked on during their residency (which can last up to several months). The real reward, though, are the innovative and unexpected ways these creative minds find to use that equipment.
We met with four of these artists in Autodesk’s workshop to see what they’ve come up with, and will be profiling one of them each day this week.

John Whitmarsh didn’t set out to be a sculptor, but it’s clear he’s exactly where he should be. The 41-year-old California native originally attended Syracuse university for film school, but after graduation quickly found a much greater interest in sculpture.
Having never taken any actual sculpture classes in school, Whitmarsh honed his craft as most self-taught artists do: reading books, watching videos, going to stores and simply asking for advice whenever possible. During this time he mainly worked in construction doing tile installation for residential remodels. This went on for the better part of 10 years, dividing his time between art and sculpture in the studio and high-end kitchen and bathroom remodels to pay the bills.
“The first couple years of doing it, nothing really turned out that nicely at all,” Whitmarsh explained. “Everything just didn’t look very good.” But while things were rocky to start, Whitmarsh’s sculpture work continued to grow and improve, and he’s now spent a handful of years focusing on art alone.
Whitmarsh was turned on to the Artist In Residence program by Noah Weinstein, a creative programs manager at Autodesk whom he met while selling some of his equipment. “I met Noah Weinstein because he bought a drill on craigslist that I was selling,” Whitmarsh said. “When I applied for it, it was actually in the old office — now that I’m here I’ve realized like, ‘Wow, this is ten times better.'” Better is right. The new Autodesk workshop has opened a world of possibilities for the sculptor, who usually works with wall installations — a choice he said stems from the premium on floor space in densely populated cities.

One of Whitmarsh’s main projects is a large shelving unit with handwritten text cutouts and inserts which together create an embossed look. He wanted to use his actual handwriting, but after an attempt using Livetrace—a software that converts bitmaps into vectors—produced files requiring too much cleanup, he resorted to rewriting the entire thing on a Wacom tablet.
Once he had vector files for the text, Whitmarsh used a Shopbot CNC-router—one of the workshop’s computer-controlled woodworking machines—to cut the lettering out of plastic cutting board material. He then used the same vector file to cut a large sheet of steel on the workshop’s waterjet cutter, specifying a very slight offset to allow for the plastic lettering to fit in.

Outside of wall sculpture, Whitmarsh enjoys the aesthetic look of things coiled and bundled upon themselves—a “rat’s nest,” he calls it—such as the look of rebar that has been crushed and compacted after the demolition of a building or freeway. However in many cases, recreating such a thing in the studio would be essentially impossible.
“I like exploring the physicality of materials,” Whitmarsh explained, noting how people often wonder how he twisted or bent a seemingly unbendable piece of metal, only to realize it’s not metal at all. Take an I-beam for example—normally used as a support beam in a building’s structure, I-beams are, more or less by definition, unbendable. But using 3D modeling software, an I-beam shape can be twisted or bent, then—using a 5-axis router—cut from wood or some other material.

“People look at this and say, ‘How did you twist the metal? It must have taken a ridiculous amount of force—how did you do that?'” Whitmarsh said. “It looks really heavy, but then they touch it and realize it’s actually very light.”
But while access to the workshop has allowed him to easily pursue and complete these such projects, Whitmarsh said he doesn’t like using a computer aided machine “just because you can.”
“My idea is to do things the simplest way possible,” he said. This might mean casting a mold instead of 3D printing an object, or vice versa if you can’t cast it or don’t want to spend time making a mold for a single object. “It all depends on whatever is the simplest way. A lot of times using computer aided machines would be the simplest way, but if there’s a better way, then that’s how I do it.”

While Whitmarsh never really put his film degree to good use, his original interest in visual media has begun to creep back in, especially with the degree to which modern video equipment has simplified the entire filmmaking process. “It’s mainly taking the shape of documenting my work and getting videos together of the actual making-of process,” he said. “I think people are really interested in the process behind it.”
“They have no idea what it takes to actually make something—they just see the end result, and they don’t realize how many tools and screw-ups and everything went into it.”
One thought on “Maker Profile: John Whitmarsh’s Mixed Media Sculptures”
Leave a Reply
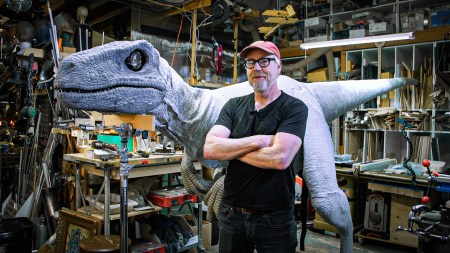
One Day Builds
Adam Savage’s One Day Builds: Life-Size Velocirapt…
Adam embarks on one of his most ambitious builds yet: fulfil…
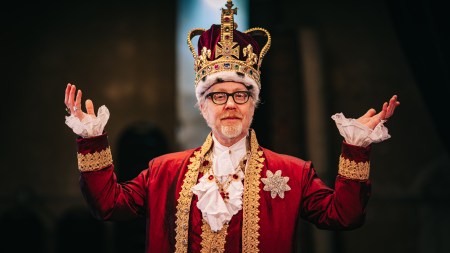
Show And Tell
Adam Savage’s King George Costume!
Adam recently completed a build of the royal St. Edwards cro…
All Eyes On Perserverance – This is Only a Test 58…
We get excited for the Perserverance rover Mars landing happening later today in this week's episode. Jeremy finally watches In and Of Itself, we get hyped for The Last of Us casting, and try to deciper the new Chevy Bolt announcements. Plus, Kishore gets a Pelaton and we wrack our brains around reverse engineering the source code to GTA …
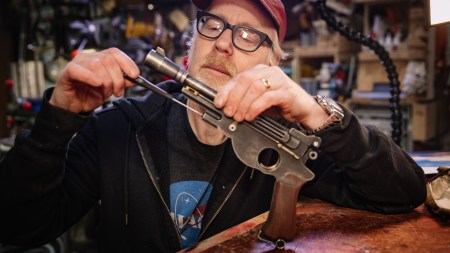
One Day Builds
Mandalorian Blaster Prop Replica Kit Assembly!
Adam and Norm assemble a beautifully machined replica prop k…
House of MCU – This is Only a Test 586 – 2/11/21
The gang gets together to recap their favorite bits from this past weekend's Superb Owl, including the new camera tech used for the broadcast and the best chicken wing recipes. Kishore shares tips for streamlining your streaming services, and Will guests this week to dive into the mind-bending implications of the latest WandaVision episod…
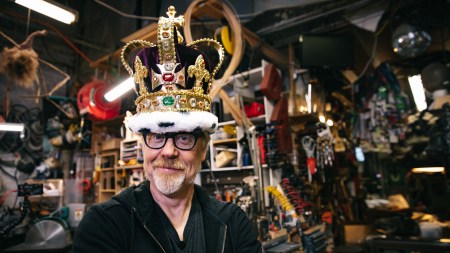
One Day Builds
Adam Savage’s One Day Builds: Royal Crown of Engla…
One of the ways Adam has been getting through lockdown has b…
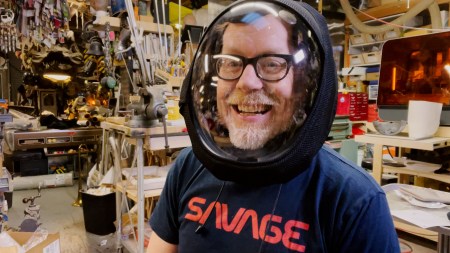
Making
Adam Savage Tests the AIR Active Filtration Helmet…
Adam unboxes and performs a quick test of this novel new hel…
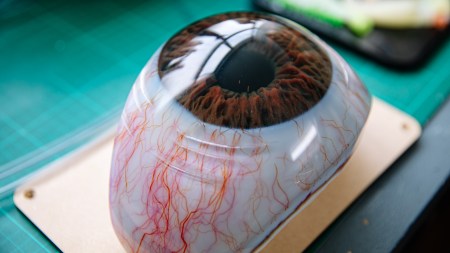
Making
Weta Workshop’s 3D-Printed Giant Eyeballs!
When Adam visited Weta Workshop early last year, he stopped …
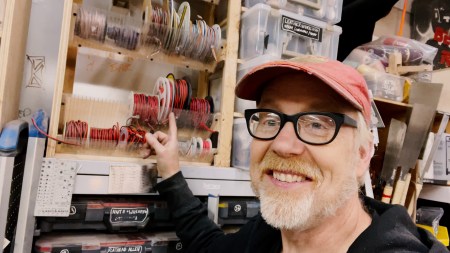
One Day Builds
Adam Savage’s One Day Builds: Wire Storage Solutio…
Adam tackles a shop shelf build that he's been putting off f…

Show And Tell
Mechanical Dragonfly Automata Kit Build and Review
Time for a model kit build! This steampunk-inspired mechanic…
I love his work. I have been into mixed media since before I knew what that meant.