How To Make Shiny Metal Prop Finishes
Bill Doran walks us through the painting process of his Rey Blaster prop from Star Wars: The Force Awakens.
Over the last month or so, I’ve been plugging away at building a replica of Rey’s LPA NN-14 Blaster Pistol from Star Wars: The Force Awakens. I suspect that the prop in the movie was made from a combination of found objects and milled aluminum parts. Mine, on the other hand, was made from scratch and cast with urethane resin parts. This made achieving a similar, convincing metallic finish a bit of a challenge. There are lots of different ways to finish resin parts to look like metal. I could have gotten the pieces chromed or vacuum metalized, but those processes are a bit cost prohibitive. On the other end of the spectrum, I’ve had less than stellar results with rattle can “chrome” paints. So instead I opted for an airbrushed finish!

I’ve dabbled a bit with Alclad II metallic lacquer paints in the past and have been looking for an excuse to get more familiar with them. This project provided the perfect opportunity to expand my paint collection a bit further and do some experimenting. Their paints are generally used together in a set of two or three combined finishes. To get a real metallic “shine” it’s necessary to lay down your metal paint on a glossy black finish. You also want a way to protect that finish once it’s all done. So I went with their glossy black finish, the “polished aluminum” paint, and their Aqua Gloss clear sealant.

Note: All of this finishing work, aside from the priming, was done with an airbrush. I like my Iwata Eclipse gravity fed brush for this kind of work.
Texture
The thing that’s going to sell an “almost chrome” finish more than anything is the ultimate texture you end up with. You want the surface to be as glass smooth as possible. In my experiments, I found that this was easier said than done.

The texture of your piece will have an impact at every step of the finishing process. This means you need to sand the piece down nice and smooth once it comes out of the mold. For the final version of Rey’s blaster, I ended up getting it to a 400 grit level, though I could have pushed it further.
After getting the plastic prepped, everything was primed. I used a rattle can primer for this, but Alclad has some of their own that I want to try the next time I paint one of these guns. I added a couple of light layers of primer paint and it looked pretty good, but I bet I could have sanded it again.

Side note: I tell myself “I bet I could have sanded that at least one more time.” on nearly every one of my prop projects.
Glossy Black Base
With the surface ready for paint, I started with that shiny gloss black in my airbrush. I didn’t want to drench the surface on the first coat, so I went with a nice, light, even pass. This was a little bit misleading, since the layer didn’t completely cover all of the primer. It looked a little bit like I had just added a whole bunch of unwanted texture, but this progressive method meant each layer would dry much faster.

The second layer of black glossy paint could be a bit more aggressive. My goal was to lay down a good amount of coverage without spraying on so much paint that it would sag. You can always add more layers of paint, but it’s a real bummer when you need to remove them.

I ended up adding three good layers of the glossy black paint. They’re lacquers, so they dry pretty quickly. I would give each layer a good 10-15 minutes to dry before adding the next round. I think this is definitely an area where practice would make a big difference in the final outcome. My finish was a little bit inconsistent between pieces.

Fisheyes
Speaking of inconsistencies, some of my parts got the dreaded “fisheyes”. These are small pockmarks where the paint avoids filling that particular layer. It has the effect of adding texture where I was trying to remove it. In this case, I think the fisheyes were caused by a combination of my not sanding the primer layer more smooth and my over enthusiastic airbrushing style. Again, this is an area where practice can make a big difference.

Glossy Insurance
Before spraying down my metallic lacquers, I hit everything with a couple layers of Alclad’s Aqua Gloss clear paint. This is meant as a final protective coat for these paints, but it also works marvelously as a base coat to help achieve a more shiny metallic sheen. It’s really thin and looks milky white in the bottle, but dries crystal clear. It also has a blue tint once it’s sprayed onto your black surface, but again, dries clear.

I added two good coats of the gloss clear onto all of my parts. I could tell that some of my pieces weren’t at the texture that was perfectly ideal and the addition of these glossy layers actually helped a little bit. Again though, I really should have sanded it just one more time.
There are lots of factors that can affect how your airbrushed paint interacts with the surface you’re applying it to. Temperature and humidity are two things that can make a big impact on the resulting finish. Since I work in my basement and this job was done in February in Seattle, it was a little bit chilly (63℉) while I worked. This most definitely played a role in the outcome of my paint job.

There are also plenty of other paints you could use to achieve this gloss finish. Catalyzed, clear urethane is a popular one. This is a bit more involved process, requiring an HVLP system. Since the paint cures via a chemical reaction, you can apply a nice, thick layer and it will cure no matter what.
Let’s Get Metal
Before committing to your final, metal paint, now is the time to decide if you’re happy with the texture on your parts. If not, it’s time to let it all dry for a day, then wet sand it down to the desired texture. This is really nitpicky, but if you have a very specific finish you’re trying to achieve, the extra work is worth it.
I decided that I was relatively satisfied with my texture, so I moved forward. With a shiny black finish achieved on my space gun parts, I could finally spray on the metal finish. I loaded up my airbrush with the “polished aluminum” Alclad paint and simply sprayed it onto my parts. This is actually the easiest part of the process. The lacquer is very thin and covers very well. One good coat is all you need to get the look you’re after.

This part of the project went very quickly. It’s also really satisfying to see your surface transformed from a dark black piece of plastic into a shiny piece of metal. A little bit of this paint goes a long way, which is great since it’s $9 for a 1oz bottle from my local hobby store.

Once the lacquer dried, I could go over the whole surface with more of that Aqua Gloss to seal and protect it. Not only does this give it a little extra shine, but it does a great job of protecting your finish. I found out (the hard way) that the oil paints I used to weather this gun would strip the metallic lacquer right off. The following photo was a test piece that failed miserably. I learned a lot from failure.

The Aqua Gloss finish completely protected the lacquer below and I was able to weather the gun to my heart’s content!

Reflecting on my Metal Finishes
Overall I’m pretty happy with how the finish turned out on this particular project, but I know I have a lot of room to grow with this particular painting system. Since I made a mold of these gun parts, I can experiment until I’m completely happy with the results. Heck, I might even try to get the parts chromed for real! I’m also planning on trying to “cold cast” all of these parts to get a more authentic aluminum finish. I’ve already done some preliminary tests and the results are promising. Since this surface can be buffed and polished, I can be a lot more aggressive about achieving the texture I desire.

I hope you’ve enjoyed this little foray into metallic finishes for your prop projects. I highly recommend you go out and experiment yourself to see what sort of paint effects you can achieve. Alcald paints are fantastic and they have a wide range of colors and effects available. If you haven’t already, look into molding and casting so that you can pop out plenty of resin copies of whatever it is you’re replicating so that you have lots of pieces for practice. We’ve got a whole series on molding and casting for you to check out on YouTube, too!

12 thoughts on “How To Make Shiny Metal Prop Finishes”
Leave a Reply
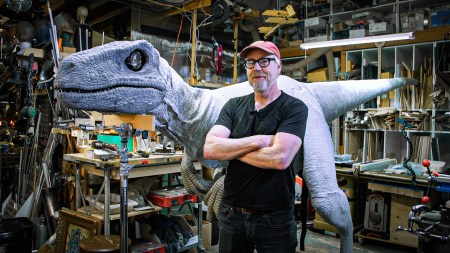
One Day Builds
Adam Savage’s One Day Builds: Life-Size Velocirapt…
Adam embarks on one of his most ambitious builds yet: fulfil…
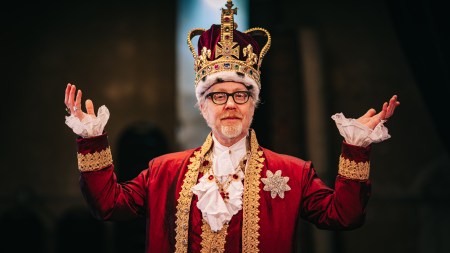
Show And Tell
Adam Savage’s King George Costume!
Adam recently completed a build of the royal St. Edwards cro…
All Eyes On Perserverance – This is Only a Test 58…
We get excited for the Perserverance rover Mars landing happening later today in this week's episode. Jeremy finally watches In and Of Itself, we get hyped for The Last of Us casting, and try to deciper the new Chevy Bolt announcements. Plus, Kishore gets a Pelaton and we wrack our brains around reverse engineering the source code to GTA …
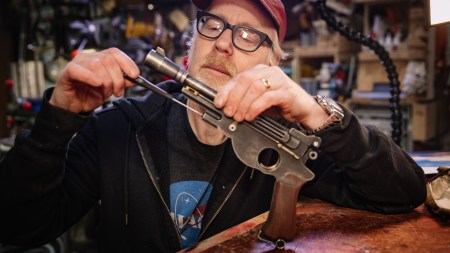
One Day Builds
Mandalorian Blaster Prop Replica Kit Assembly!
Adam and Norm assemble a beautifully machined replica prop k…
House of MCU – This is Only a Test 586 – 2/11/21
The gang gets together to recap their favorite bits from this past weekend's Superb Owl, including the new camera tech used for the broadcast and the best chicken wing recipes. Kishore shares tips for streamlining your streaming services, and Will guests this week to dive into the mind-bending implications of the latest WandaVision episod…
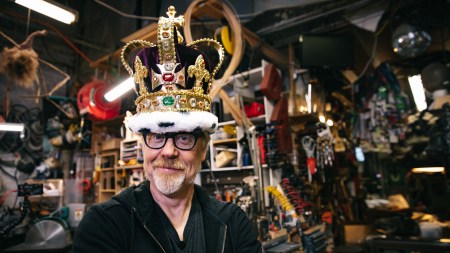
One Day Builds
Adam Savage’s One Day Builds: Royal Crown of Engla…
One of the ways Adam has been getting through lockdown has b…
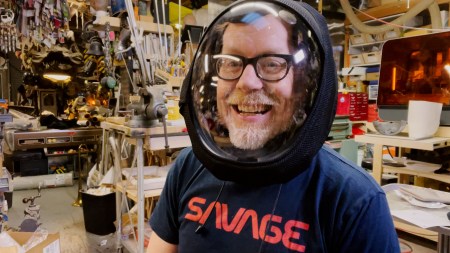
Making
Adam Savage Tests the AIR Active Filtration Helmet…
Adam unboxes and performs a quick test of this novel new hel…
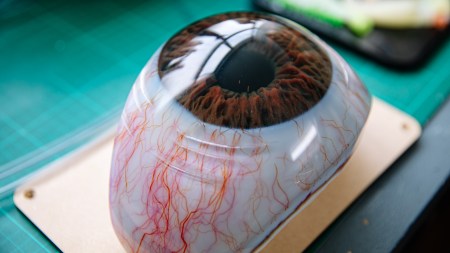
Making
Weta Workshop’s 3D-Printed Giant Eyeballs!
When Adam visited Weta Workshop early last year, he stopped …
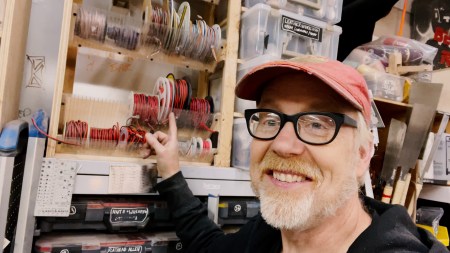
One Day Builds
Adam Savage’s One Day Builds: Wire Storage Solutio…
Adam tackles a shop shelf build that he's been putting off f…

Show And Tell
Mechanical Dragonfly Automata Kit Build and Review
Time for a model kit build! This steampunk-inspired mechanic…
Fisheyes are usually caused by an oily contaminant on the surface or in the paint. Remnants of a silicone mold release can cause them or, judging from the size and uniformity of the fisheyes you experienced a more likely cause is oil vapor in the air lines. Do you use an oil trap on your compressed air system, not just at the compressor but also at the end where the airbrush hose plugs in?
Arts Great tips! I do not have an oil trap on my compressor. I’m looking to upgrade my airbrush compressor anyway, so I’ll be sure to get one of those too. Thanks! =D
niiiiiiice! i want a casting, Bill!
Great stuff. I’ve been tempted to try alclad paints for my stainless steel Ho Scale passenger cars as the usual methods fall short of looking very good.
Getting a trap is a good idea even if the compressor is oiless because getting water in your lacquer paint can create the same kind of bubbles.
Thanks for this Bill! Great to see more detail on this. I have been following the build on Youtube. And a big thanks for the casting and molding series , its been great.
Thank you very much for this Bill. Your videos and write up are a fantastic resource. The best part is the names of techniques you have, simply knowing the metallic technic in mold making is called “cold casting” has opened up a huge rabbit hole of info on google.
Can I ask, is there any reason on this particular prop, why you didn’t create the seams where they’d fall on the model if it were build from separate parts. Or if there was any reason why the model wasn’t broken up into more parts to hide the seams easily?
Thanks for the write-up Bill, great to see this project finished. I’m very impressed with the quality of the metallic finish, might have to use these techniques on a future project. Which looks more like metal in person: this, or cold casting?
You’re welcome!
I definitely could have broken up the model into more parts. It just depends on how much time you might want to spend on it overall.
I personally like the cold cast look better for this application, it just isn’t always the most feasible option. The paint process can be applied to any surface, making it really handy to know.
are you doing any more castings of this blaster? I’ve been looking for one and this looks great.
are you making casts available still. Know this was about a year ago. Have been looking around for a casting and came across this today. Looks great!