Tested Builds: Fallout 4 Mini Nuke Kit, Part 1
We kick off a new build this week, this time tackling a 3D-printed model kit designed by Jacky Wan. This Fallout 4 Mini Nuke model is a cross-section, showing off the beautifully imagined interior of the device and printed by Sean with our Ultimaker 2 desktop 3D printer. Frank is also in-house to assemble a kit and teach us how to paint it! (This first video is available for everyone–watch the rest of the build by signing up with the Tested Premium member community!
16 thoughts on “Tested Builds: Fallout 4 Mini Nuke Kit, Part 1”
Leave a Reply
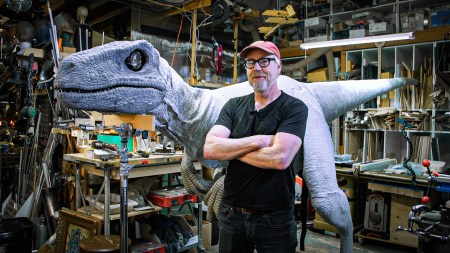
One Day Builds
Adam Savage’s One Day Builds: Life-Size Velocirapt…
Adam embarks on one of his most ambitious builds yet: fulfil…
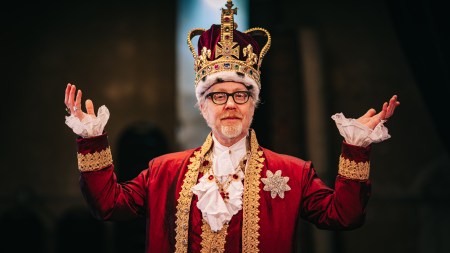
Show And Tell
Adam Savage’s King George Costume!
Adam recently completed a build of the royal St. Edwards cro…
All Eyes On Perserverance – This is Only a Test 58…
We get excited for the Perserverance rover Mars landing happening later today in this week's episode. Jeremy finally watches In and Of Itself, we get hyped for The Last of Us casting, and try to deciper the new Chevy Bolt announcements. Plus, Kishore gets a Pelaton and we wrack our brains around reverse engineering the source code to GTA …
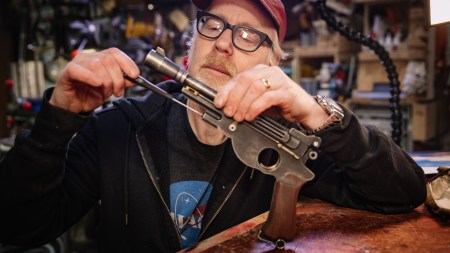
One Day Builds
Mandalorian Blaster Prop Replica Kit Assembly!
Adam and Norm assemble a beautifully machined replica prop k…
House of MCU – This is Only a Test 586 – 2/11/21
The gang gets together to recap their favorite bits from this past weekend's Superb Owl, including the new camera tech used for the broadcast and the best chicken wing recipes. Kishore shares tips for streamlining your streaming services, and Will guests this week to dive into the mind-bending implications of the latest WandaVision episod…
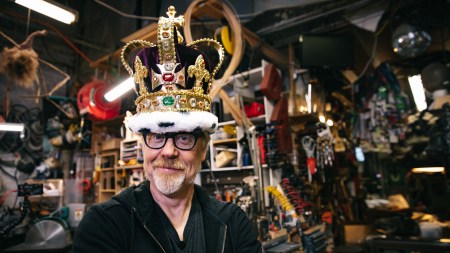
One Day Builds
Adam Savage’s One Day Builds: Royal Crown of Engla…
One of the ways Adam has been getting through lockdown has b…
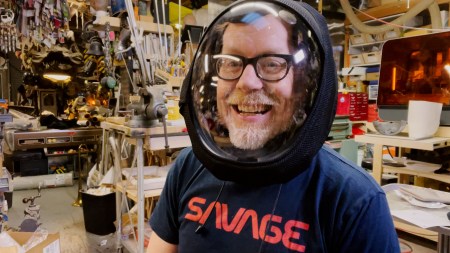
Making
Adam Savage Tests the AIR Active Filtration Helmet…
Adam unboxes and performs a quick test of this novel new hel…
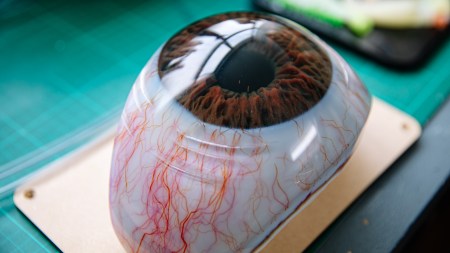
Making
Weta Workshop’s 3D-Printed Giant Eyeballs!
When Adam visited Weta Workshop early last year, he stopped …
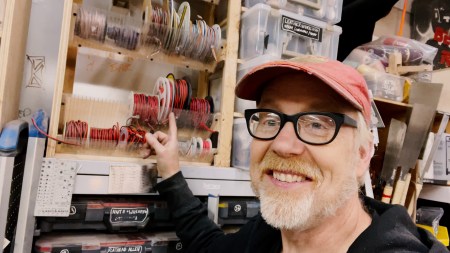
One Day Builds
Adam Savage’s One Day Builds: Wire Storage Solutio…
Adam tackles a shop shelf build that he's been putting off f…

Show And Tell
Mechanical Dragonfly Automata Kit Build and Review
Time for a model kit build! This steampunk-inspired mechanic…
Is the premium player natively Chromecast compatible yet I am looking forward to this and Adams videos but I would rather watch them on my TV than my laptop or phone and doing through the web browser all ways get sync problems. Thanks for th great job and videos keep it up
This is a beautiful kit and I look forward to watching you guys putting it together. Are there any fume considerations for using cyanoacetate with ABS and other 3DP materials?
I ask because I have first hand experience of faulty fume hoods and super glue releasing noxious fumes from different materials; making me super cautious.
frank’s toothpaste trick sounds like a variation of something i had read a few years ago: practically the same principle, but using coarse salt on a slightly wet surface for the masking. you could push the salt clumps around with a toothpick before painting, and they’re supposed to make shapes like a compound of several crystalline flakes, just like paint chips.
other than that: guuuuuys, i *want* to throw money at you! will we eventually get paypal as an option?
Great to see another model build , getting closer to a space ship build, is there any way we can see Adam in a week of builds weathering a spaceship
I ran into the capillary action problem with painting routered plywood. I found that hitting the plywood with a quick coat of a “clear coat” sealed up the pores/channels and made it so that the paint would stay where you put it. Would the same work for 3D prints?
I think it generally depends on scale. The salt method is good for scale models, say on a military fighter jet or a tank in 1/72 or 1/32 scale. For larger chips in a more 1:1 scale, the toothpaste technique is probably better.
For scale stuff, there’s also this stuff called Ammo of Mig Heavy Chipping Effects and also Scratches Effects
Spray your base color, let it dry, then spray this fluid over it. Let it dry for a few min. Then spray your top coat. Let that dry for a few min. Then, using a brush wet with water. lightly start brushing. The water reactivates the fluid and it begins to start chipping and scratching away. You can also use a toothpick to make some more deliberate scratches.
That stuff is similar to the hairspray technique. Instead of that product, use regular plain hairspray and tooth pick. I don’t know how well the brush works with it though – I’ve only done this one with a toothpick
now that you mention it, i think it was on scale models. makes sense, too, given that there is only a certain spectrum of paint chip scale to be had from easily available household salts.
but i’ll be damned if the inventiveness of the scale modelling community doesn’t amaze me whenever i read something about their techniques. (and the dedicated products for what often looks like borderline absurd niches)
Download Jacky’s full Mini Nuke here: https://www.youmagine.com/designs/fallout-4-mini-nuke-redicubricks
The cutaway kit is available here: http://shop3d.ca/product/fallout-4-mini-nuke-with-internals-unfinished-model-kit/
Read more about how Jacky made the Nuke here: https://ultimaker.com/en/blog/19397-designing-3d-printing-and-painting-the-fallout-4-mini-nuke
Hi Norm, I can’t help but notice that you are sporting a Pebble Time for about a while now.. has it became your ”go to” smartwatch?
it sure is the perfect one for me.. not too much bling and efficient at what its supposed to do.
do you miss android wear? I would be interested to ear your toughts on that matter.
Sean, you mention slowing the printer down on small/complex shapes to stop stringiness of the plastic. What would be a good print speed to do this at? If it helps I have a Makerbot Replicator 2.
I don’t recall exactly what I was saying but… it depends on the print. For stringing I may actually lower the temperature so it doesn’t string us much. Retraction settings can also make a difference. For small details I would slow it down which might also involve lowering the temperature. This is where it can get frustrating to dial in prints since so many factors depend on each other. But to answer you question, if I’m doing something really fine, I might go as low as 30 mm/s, you can go even slower, won’t hurt anything. Look for settings in your slicer like ‘minimum time per layer’ sometimes you can set a threshold, that if a layer takes less that x amount of time to ‘draw’ it will slow to allow the plastic to cool.
Damnit! I still haven’t picked up one of these yet! Would have been cool to follow along. 8]
At around the 9:55 mark Frank mentions painting the “Nerf gun stuff”. Does anybody know what he is talking about. Did they upload a video on here showing the process?
I think he may have been talking about this: http://mdvip-tested.md-staging.com/art/540874-making-sci-fi-armor-video-game-trailer/
Mine would have looked a lot worse with out your videos,Thanks Guys!
Thank you Frank for the key that unlocked a whole section of google for me. “catalyst spray poly primer” is the word of the day, even “Spray Poly Primer” has helped.
For years I’d been using 10+ coats of regular spray paint on 3D prints to smooth and seal them, before I was given a can of spray bog filler, or auto filler – which was the product name. I’ve been telling friends and students about this but end up with blank looks as they head to the hardware stores and paint stores that don’t know the product.
Now I can search it and have found a local store, but also a cheaper online supplier. So thanks again!