Hands-On with Formlabs’ Fuse 1 SLS 3D Printer!
We visit the headquarters of Formlabs, makers of the Form 2, to check out their newest 3D printer. The Fuse 1 is a SLS printer, which can make highly detailed and complex models with nylon using a process that has not been accessible to prosumers. Sean gets an in-depth look at the Fuse 1, several of its prints, and sends one of his own models through the SLS process to inspect its print quality! (Disclaimer: Formlabs provided our travel for this preview trip.)
17 thoughts on “Hands-On with Formlabs’ Fuse 1 SLS 3D Printer!”
Leave a Reply
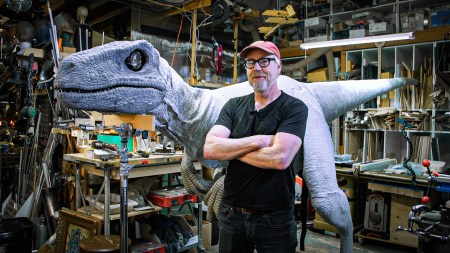
One Day Builds
Adam Savage’s One Day Builds: Life-Size Velocirapt…
Adam embarks on one of his most ambitious builds yet: fulfil…
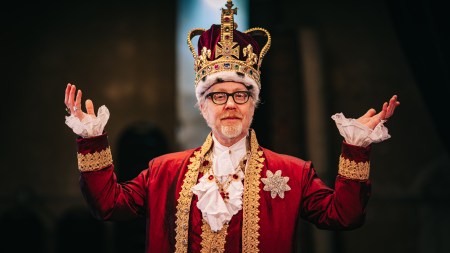
Show And Tell
Adam Savage’s King George Costume!
Adam recently completed a build of the royal St. Edwards cro…
All Eyes On Perserverance – This is Only a Test 58…
We get excited for the Perserverance rover Mars landing happening later today in this week's episode. Jeremy finally watches In and Of Itself, we get hyped for The Last of Us casting, and try to deciper the new Chevy Bolt announcements. Plus, Kishore gets a Pelaton and we wrack our brains around reverse engineering the source code to GTA …

Making
Adam Savage in Real Time: God of War Leviathan Axe…
Viewers often ask to see Adam working in real-time, so this …
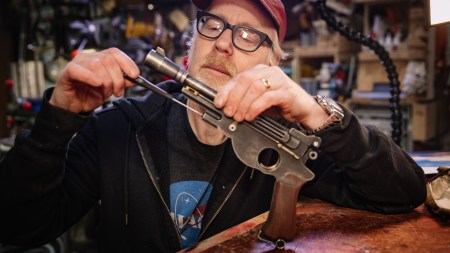
One Day Builds
Mandalorian Blaster Prop Replica Kit Assembly!
Adam and Norm assemble a beautifully machined replica prop k…
House of MCU – This is Only a Test 586 – 2/11/21
The gang gets together to recap their favorite bits from this past weekend's Superb Owl, including the new camera tech used for the broadcast and the best chicken wing recipes. Kishore shares tips for streamlining your streaming services, and Will guests this week to dive into the mind-bending implications of the latest WandaVision episod…
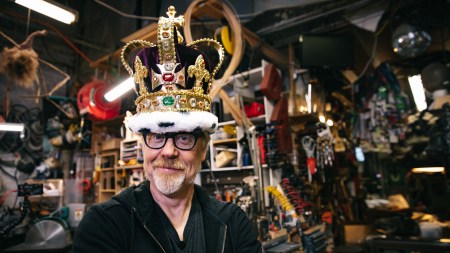
One Day Builds
Adam Savage’s One Day Builds: Royal Crown of Engla…
One of the ways Adam has been getting through lockdown has b…
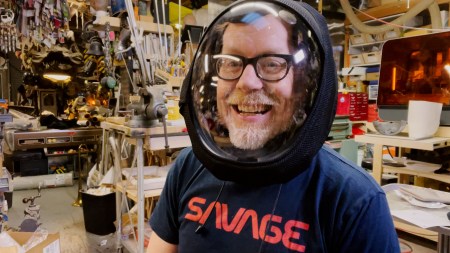
Making
Adam Savage Tests the AIR Active Filtration Helmet…
Adam unboxes and performs a quick test of this novel new hel…
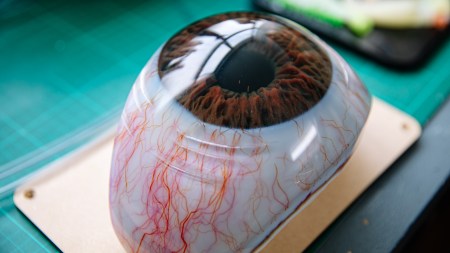
Making
Weta Workshop’s 3D-Printed Giant Eyeballs!
When Adam visited Weta Workshop early last year, he stopped …
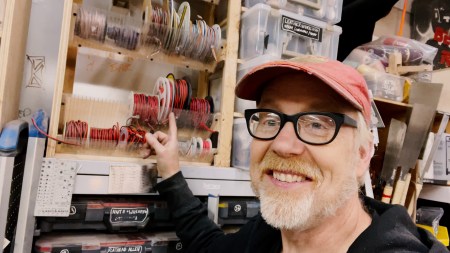
One Day Builds
Adam Savage’s One Day Builds: Wire Storage Solutio…
Adam tackles a shop shelf build that he's been putting off f…
This looks really amazing.. such impressive technology. One thing I’ve always wondered about with powder- and liquid-based printing: I’m assuming that you can’t print things that are water tight. Otherwise how do you get the unused material to drain out?
I’m guessing the holes in the bottom of your buckaroo banzai car are for just that purpose.
This looks amazing, though obviously too expensive for the average consumer. At $20k you need to be doing some business for it to make sense.
I wouldn’t be surprised to find that the product designers at my company have put their names down, though. We already have several Form One, a Form Two and two giant, older SLS printers, but they can’t keep their hands off a new tool 🙂
I am so jealous of Sean’s job. To go play with this printer in Boston would have been amazing. I love the print and material quality from the Fuse 1. I can’t wait to see what Sean gets to print when Tested finally gets one in house!
A correction – the Fuse 1 is not the first benchtop SLS printer priced well under the typical $150K+ price tag. The Swiss-made Sintratec Kit came out toward beginning of 2016 for $5600. It’s a kit that takes approx 4 days to build with a volume of 110mm x 110mm x 110mm. They also offer the S1 which is fully assembled for $10,135 with a volume of 130mm x 130mm x 180mm.
The Fuse has a volume of 165mm x 165mm x 320mm for $9,999.
So basically it’s the strength of the material + the support that sets it apart right? As the detail is not perse as good as some way cheaper regular 3D printers, looking at the licence plate of Sean’s model for instance. For me this would be perfect as I need a printer for structural components, but for great detail I guess regular printers are still the way to go.
Looking forward to watching this but I just have to say that seeing the Jetcar in my news feed always brings a big smile to my face!
Yep. Strength, volume, support structures and price per part are the up side. Since the powder supports everything you can print stuff that would be really difficult (ie: see us trying to print Zorg ZF1). The nylon is really strong and even has some give to it. I don’t have figures yet, but the SLS parts will be cheaper than SLA. You can also pack a ton of parts into one print job and even add more as it’s printing. The surface finish and detail will not be as good as SLA but is still very good. It’s just a different tool, need to pick what works best for you.
Thanks for the extra info! Really great for small businesses and it does indeed look like that interactive system is really smooth and versatile. It would be nice for my hobby in astronomy to be able to print small gears and precise fitting adapters.
this looks like a really interesting machine indeed.
but i have the same question as berjb: closed-off hollow shapes are a problem, right? if you wanted something hollow, you need an opening to pour out the powder from inside. and the spectrum of weight vs structural support you get with different infill patterns sounds like a total nightmare in sls, right?
Yes you need a ‘drain hole’ this is true on pretty much anything other than FDM. Unlike FDM where you can specify the infill density, anything that is ‘solid’ on the 3D model will print solid in other printing technologies. If you want something hollow you have to build the model that way. You could technically print the model with no drain hole, but it would trap loose powder inside. For small areas, no big deal, but larger areas would add weight and be wasteful.
thanks sean. 🙂
with variable infill, i was thinking about things like plane wings, for example, where i can imagine a demand for tweaking stiffness vs mass along the piece – with sls, it looks like you’d have to print it in parts to offset the closedness of the volume.
$10,000. You know, a normal person price.
MInd Blown!
It’s definitely a very amazing printer, and would come in very handy for certain companies. Instead holding inventory on hand, they can have digital inventory and convert that to a real life product when needed.
Definitely the way for the future, and it’s very cool it’s getting more accessible now.
it’s completely reasonable for someone starting up a small production business. Would pay for itself quickly.
Not unlike a quality mill or lathe.
Not just for a production business either. Any hardware startup that is making something structural at about the size of a toaster, and doing the industrial design inhouse, would break even on this thing within 4-5 prototype casings. It gets very expensive to outsource these things once you factor in the whole process, like time spent dealing with vendors, waiting for parts and potential for QA issues.