The Stop-Motion Puppets of Aardman Animations!
Adam Savage visits Aardman Animations’ workshop to get up close with some of the beautiful stop-motion animation puppets used in the studio’s upcoming film Early Man. Aardman senior model maker Jimmy Young walks us through some of the modelmaking processes that go into these puppets’ sculpts, clothes, and armatures!
12 thoughts on “The Stop-Motion Puppets of Aardman Animations!”
Leave a Reply
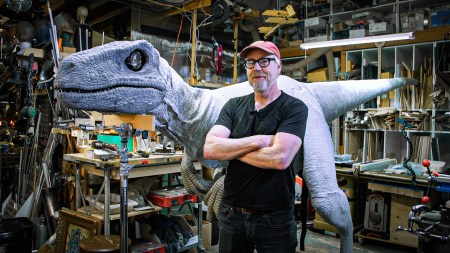
One Day Builds
Adam Savage’s One Day Builds: Life-Size Velocirapt…
Adam embarks on one of his most ambitious builds yet: fulfil…
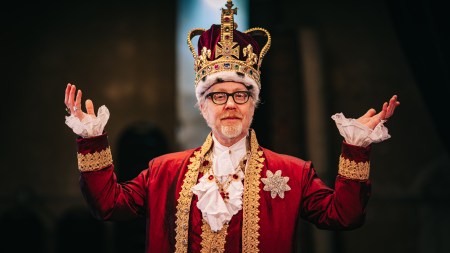
Show And Tell
Adam Savage’s King George Costume!
Adam recently completed a build of the royal St. Edwards cro…
All Eyes On Perserverance – This is Only a Test 58…
We get excited for the Perserverance rover Mars landing happening later today in this week's episode. Jeremy finally watches In and Of Itself, we get hyped for The Last of Us casting, and try to deciper the new Chevy Bolt announcements. Plus, Kishore gets a Pelaton and we wrack our brains around reverse engineering the source code to GTA …
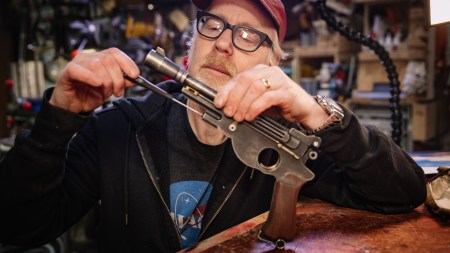
One Day Builds
Mandalorian Blaster Prop Replica Kit Assembly!
Adam and Norm assemble a beautifully machined replica prop k…
House of MCU – This is Only a Test 586 – 2/11/21
The gang gets together to recap their favorite bits from this past weekend's Superb Owl, including the new camera tech used for the broadcast and the best chicken wing recipes. Kishore shares tips for streamlining your streaming services, and Will guests this week to dive into the mind-bending implications of the latest WandaVision episod…
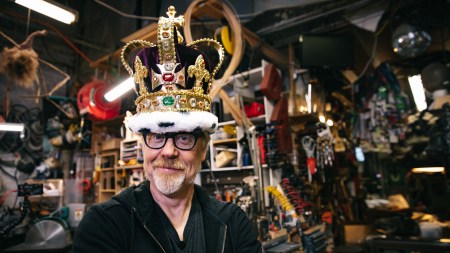
One Day Builds
Adam Savage’s One Day Builds: Royal Crown of Engla…
One of the ways Adam has been getting through lockdown has b…
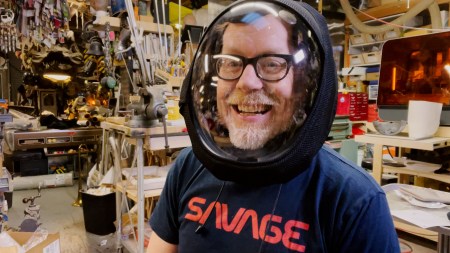
Making
Adam Savage Tests the AIR Active Filtration Helmet…
Adam unboxes and performs a quick test of this novel new hel…
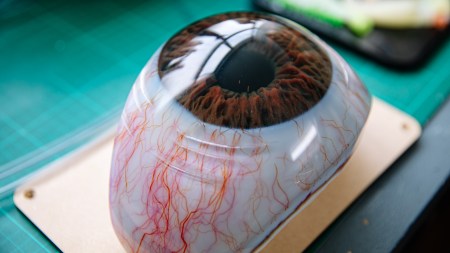
Making
Weta Workshop’s 3D-Printed Giant Eyeballs!
When Adam visited Weta Workshop early last year, he stopped …
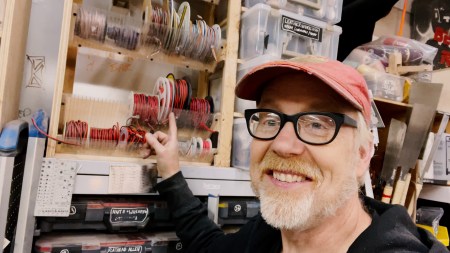
One Day Builds
Adam Savage’s One Day Builds: Wire Storage Solutio…
Adam tackles a shop shelf build that he's been putting off f…

Show And Tell
Mechanical Dragonfly Automata Kit Build and Review
Time for a model kit build! This steampunk-inspired mechanic…
That was amazing. Well done. I could definitely watch a lot more of that.
Love that SKX007 pepsi bezel. It’s a great travel beater.
The armature is also very cool.
Really amazing work – Can’t wait for the rest of this series.
Jimmy, if you’re reading comments here, what is the K&S system you mentioned a few times that are used for attaching hands and the like? I had a bit of a look around and it seems K&S are a brand and there’s some square tubing that crops up in a few places. Is it literally just a rod that friction fits into a tube or is it a specific system?
Hi yes your right. K&S is a brand name. I think it maybe an American brand name, but I’m not sure. we keep calling it that because way back on chicken run that’s all you could get hold of. In the UK we now buy from here http://www.albionalloys.co.uk So it is just a tube system that fits inside itself we normal use square and round, and we use loads of the stuff. Its quite easy to cut and to silver solder we also double it up for rigging points in the puppets for extra strength. I hope that answers your question and I’m glad your enjoying the series.
Perfect, I’m in the UK too so I shall check out Albion Alloys. Thanks for taking the time to reply 🙂
no problem, any other questions just drop them here or over on my Instagram page
im really curious….with so much hair and fake fur,i wonder how they keep the texture and hair from getting messed up from frame to frame?
That’s what they called “boiling”, something they keep in as part of the Aardman style. Just like not hiding the fingerprints, they like to emphasise the stop-motion-esque visual give-aways.
The hard Polyurethane molds are amazing, and very detailed. Can I ask if they are 3D printed or CNC milled, or are they made traditionally with sculpted clay around the master? The sprue, airflow, and keying looks very well thought out and even CAD modeled.
Has anyone on tested had experience with using hard molds?
Is there any problems with leaking/flashing by using a hard mold?
Are there any special techniques for fast/slow, and consistency of fluids when filling a mold with a syringe/injecting, or making sure you don’t have air bubbles trapped in the chamber as your injecting, (especially with small parts)?
Great video, I love seeing something in practice that I’ve been thinking about trialing.
-removed double post-
For more long term on the cavemen we apply the same principle but use a polyurethane mix with toloune. A bit more tricky to work with but has longer lasting results. Something you must do under controlled extraction. Hope that answers the question.
no Cad involved but thank you it’s quite the compliment. All hand made with an old school layup.
Mold making is a bit of an art, lots of rules to follow to achieve a great mold. On the molds we make flashing is kept to a minimum if any. The more flashing with have the longer it takes to sand off, and I hate silicone sanding.
You shouldn’t get any leaking unless you putting so much pressure when your filling the molds. You shouldn’t get much flashing on either hard or soft molds, again to do with pressure.
When filling molds it’s very much about flow rate and material knowledge a good mold making will know this and will enable them to make a great mold.
Thanks for the comments and good luck with making some of your own molds.