Bits to Atoms: How Carbon’s CLIP 3D Printing Technology Works
The Tested team visited Carbon HQ outside of San Francisco to see exactly how this new 'CLIP' 3D printing tech works.
Carbon3D (now going by just Carbon) has been all the buzz in the 3D printing community with their M1 printer which uses CLIP technology to greatly increase the speed and quality of DLP printing. The Tested team visited Carbon HQ outside of San Francisco to see exactly how this new tech works.

As we’ve discussed before, 3D printing with UV-cured resin tends to offer the highest level of detail and choice of material (compared to 3D printing processes like FDM). Let’s review the options. SLA (Stereolithography), such as the Formlabs Form 2, draws and cures each layer of resin using a laser. DLP (Digital Light Processing) uses video projector technology to draw and cure each layer in one blast. Polyjet uses an inkjet-like head to draw each layer on a platform and is cured via a UV light unit. Now, Carbon is introducing CLIP (Continuous Liquid Interface Production) which drastically increases printing speeds and improves surface finish–but how does it work?
First let’s look at the normal SLA or DLP printing process. The model is ‘drawn’ layer by layer via laser or projector onto a print platform and must go through a peel process after each layer. Exactly how the peel is done varies by printer and technique but it generally consists of the print platform, moving out of the way so that the resin can be redistributed for the next layer. This slows down the printing process and also requires generating support structures to hold the print steady.

Carbon’s CLIP technology eliminates the peel process by using an oxygenated layer of resin between the resin tray window and the print itself. This layer creates a dead zone which allows the print to emerge continuously from the resin tray, skipping the peel process. OK, but how does that happen? The secret is in the M1 resin tray, called a ‘cassette’ which holds the resin and has an oxygen-permeable window in the bottom which a DLP unit shines light through. Carbon won’t divulge exactly how the chemistry works but the cassette allows a resin layer between the window and where the printing happens to be oxygenated which inhibits the curing process while still allowing the DLP light to shine through and solidify the resin above. I know–it sounds crazy.

One of the big advantages of this process is a drastic decrease in print times. We observed a test print actually emerge, Terminator 2-like, albeit a little slower, from the vat of resin while we watched for 15 minutes. The M1 prints at a fixed 75 micron resolution which falls in the middle of one of my favorite pro machines–the 3D Systems ProJet 7000 HD which can produce prints at 125-50 microns resolution. And while the M1 may not go to as fine a resolution as other printers, the nature of the CLIP process tends to blur print layers to where they are much harder to notice.
Carbon did not set out to just make printing faster but to make this an actual production machine for making parts to be put directly in the field. 3D printing is often referred to as rapid prototyping as it can be used to easily make multiple iterations of a part. Often the 3D printed materials are not suitable for long-term use and must ultimately be manufactured by traditional methods. Carbon has introduced a line of industrial-grade materials that are meant to be put in direct service and have been successfully tested by companies such as BMW and Legacy Effects. The parts we saw were truly impressive such as a vent with the strength of glass-filled nylon and heat resistance up to 500℉. Or the super-flexible material which was some of the nicest I have ever seen 3D printed. Our demo print was done with the prototyping resin which is designed for exactly that – fast production of prototypes. It was a very fine print and the finish was beautiful, and although not as strong as the other resins, it was still quite sturdy.

These fancy materials do pose some challenges when printing. First, the resin cassette currently does not auto-fill, so the exact volume of the print must be calculated and that quantity of resin placed in the cassette. Second, other than the prototyping resin, most of the other resins are two-part, meaning that they must be mixed before going into the cassette. Once mixed, they immediately start to cure and must be printed with right away. This means there’s no re-using extra resin left in the cassette – part of the reason for careful measurement. Carbon said they are able to re-purpose established industrial resins which allows them to make such strong, service-ready parts but also requires the mixing process.

Post processing is the same as other resin printers–the printed part is washed in alcohol to remove any liquid resin, then ‘baked’ under UV light for the final cure. The part can be sanded or even sand blasted to smooth out any print lines and can even be painted.

Carbon envisions the M1 as an actual production machine, making ready-to-use parts and its speed helps to make that possible. However, it’s also priced for an industrial market as it’s only available to lease at $40,000 a year with a minimum term of 3 years and that’s just for the printer, two cassettes and a resin sampler pack. Training, installation and needed accessories will run you another $22,000. While expensive, if manufacturers can produce field-ready, print-on-demand parts quickly, this may not be a bad way to go.

With so much hype surrounding 3D printing, I see more and more too-good-to-be true products – everyone is making a cash grab. With Carbon, I was truly impressed with the quality of parts that the M1 produced and I look forward to see where and how the CLIP technology will be used. I can’t help but wonder if we will see it on a desktop unit any time soon. It’s this kind of tech that will keep driving 3D printing further from its rapid prototyping origins to full-blown production and custom manufacturing–pretty cool stuff.
6 thoughts on “Bits to Atoms: How Carbon’s CLIP 3D Printing Technology Works”
Leave a Reply
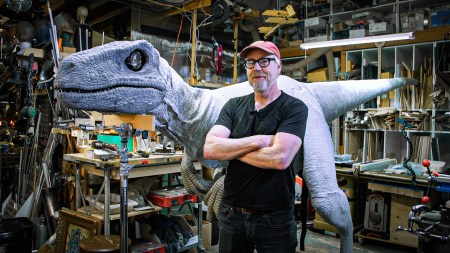
One Day Builds
Adam Savage’s One Day Builds: Life-Size Velocirapt…
Adam embarks on one of his most ambitious builds yet: fulfil…
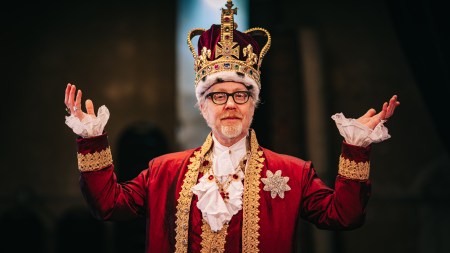
Show And Tell
Adam Savage’s King George Costume!
Adam recently completed a build of the royal St. Edwards cro…
All Eyes On Perserverance – This is Only a Test 58…
We get excited for the Perserverance rover Mars landing happening later today in this week's episode. Jeremy finally watches In and Of Itself, we get hyped for The Last of Us casting, and try to deciper the new Chevy Bolt announcements. Plus, Kishore gets a Pelaton and we wrack our brains around reverse engineering the source code to GTA …

Making
Adam Savage in Real Time: God of War Leviathan Axe…
Viewers often ask to see Adam working in real-time, so this …
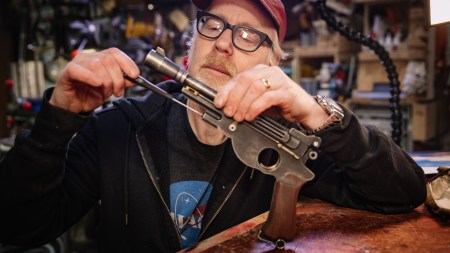
One Day Builds
Mandalorian Blaster Prop Replica Kit Assembly!
Adam and Norm assemble a beautifully machined replica prop k…
House of MCU – This is Only a Test 586 – 2/11/21
The gang gets together to recap their favorite bits from this past weekend's Superb Owl, including the new camera tech used for the broadcast and the best chicken wing recipes. Kishore shares tips for streamlining your streaming services, and Will guests this week to dive into the mind-bending implications of the latest WandaVision episod…
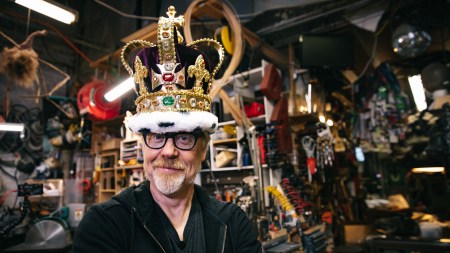
One Day Builds
Adam Savage’s One Day Builds: Royal Crown of Engla…
One of the ways Adam has been getting through lockdown has b…
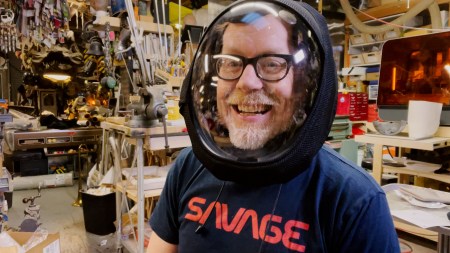
Making
Adam Savage Tests the AIR Active Filtration Helmet…
Adam unboxes and performs a quick test of this novel new hel…
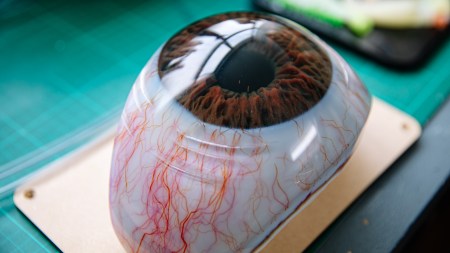
Making
Weta Workshop’s 3D-Printed Giant Eyeballs!
When Adam visited Weta Workshop early last year, he stopped …
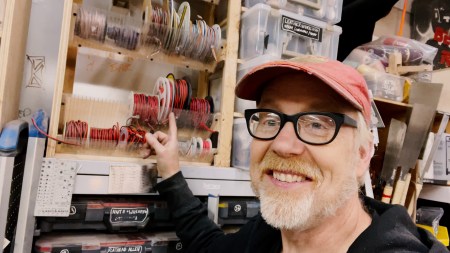
One Day Builds
Adam Savage’s One Day Builds: Wire Storage Solutio…
Adam tackles a shop shelf build that he's been putting off f…
There should be shops springing up offering prints done by this. The required $120,000 three year subscription to get one of these is kind of steep if you are not in manufacturing. No version for the maker community. The sales guys got the better of the developers just like in Silicon Valley season 3.
Sculpteo has a M1 for this purpose. https://www.youtube.com/watch?v=iPh9zJhHD8Y
But this machine is definitely marketed to big manufacturers, not the consumer/pro-sumer market. I dug into the science a bit more with some engineers there (hope to get up that podcast soon). I don’t think they’ve touched limits on speed with this process.
Sculpteo has a M1 for this purpose.
But this machine is definitely marketed to big manufacturers, not the consumer/pro-sumer market. I dug into the science a bit more with some engineers there (hope to get up that podcast soon). I don’t think they’ve touched limits on speed with this process.
Sean have you seen this machine, they claim they are even faster
http://newpro3d.com
Of course, I understand this is a big company and university item. Don’t think that there is anything specially expensive here material wise, it is all about cashing in on the unique IP. Nothing wrong with with it of course. Calculation is based on what company pay now in time and material to end up with a finished product and than take 15% off and that is your price range. Attractive as service is included and companies don’t have to worry about updates and repairs. They could easily jump to better tech if it shows up. I hope the consumer will get offered an option eventually if our less patent restricted friends figure out how it works. I bet they have chemistry that binds and releases oxygen dependent of light exposure.The post print processing maybe key here. Did you smell ozone around the printers?
If they are using Teflon AF on the cassettes as the science paper mentioned, that’s pretty pricey (>$1000/kg – not that you would need that much). But you’re generally right.
I didn’t smell ozone – thought I might from the DLP projector interacting with O2, but nothing apparent. Difficult since the resins themselves have an odor, so it may have been hidden. I was personally surprised they didn’t pressurize chamber with O2 for increased speed/dead zone. But that’s my crazy scientist mind.
The item printed was post processed and in our hands ~1 hour. I think it just went through a quick wash and UV oven cure. Sean is fiddling with the actual print item at the end.