Building a District 9 Alien Rifle Replica, Part 4
The final casting, assembly and finishing, before Bill heads to Comic-Con!
Over the past month, Punished Props’ Bill Doran built a 1:1 scale replica of the alien assault rifle from District 9 to unveil with us at Comic-Con. Bill’s build logs and videos will walk through his design and fabrication process, and his finished piece was unviled with a surprise at SDCC. Place your questions for Bill in the comments below! Here are parts 1, 2, and 3.
Here it is: the final part of the District 9 Gun Prop build! Fortunately, the molding process was fairly painless and yielded some very useful molds. When it comes to casting, having good molds can make or break a project, especially when you need 24 of something, as we did for this whacky alien gun.
Dump Molds
Most of the pieces for the gun were done with simple dump molds. This means all I had to do was mix up some Smooth-Cast 300 resin, tint it with a little SO-Strong black, and pour it into the molds we made. The only fancy business we did was to tap the mold around a bit to make sure no bubbles were trapped.

This process was used for the top scope pieces, the barrel pieces, some of the side greeblies, and all 24 of the tubes that stick out the sides of the barrel length.
Rotocasting
The large tube piece on the bottom of the gun needed to be handled in a different way. If we had just filled it up with resin, it would be extremely heavy, not to mention all of that wasted resin. Instead, we slush cast the inside of the mold with several layers of Onyx fast resin.

For a tubular shaped piece, it was actually quite easy. I dumped in a little bit of resin and then rolled the mold on the work bench surface until the inside of the mold was coated. Then I just had to keep rolling it to get an even coating of resin. We did this three to four times until there was a nice shell of resin inside the mold. It was left to cure before being demolded.

The Big Fella
For the main gun body piece, I knew we were going to have to get creative during the casting process. Like the previous tube piece, casting it solid would create a ridiculously heavy piece. I could have tried rotocasting it, and I plan to try that in the future, but for this first casting I wanted to hedge my bets and go with a solution that I knew would produce a workable piece.

I started by pouring some Smooth-Cast 300 into each side of the open mold. This way I could slush the resin around a bit and make sure there wouldn’t be any bubbles trapped in the recesses. When the resin started to kick, I laid in some insulation foam blocks that I had cut out. These floated on the resin layer and stuck to it as it cured. This way, when the mold was closed up, these foam filler pieces would stay in place when pouring the rest of the resin.

Once the resin was set up, the two mold halves were clamped together and we started filling up the remaining space with more Smooth Cast 300. This was done in stages; mixing up a cup of resin, pouring it in, and slushing it around to avoid any bubbles.

Once the resin was fully cured, we could retrieve the cast piece from the mold. I also trimmed off the pouring spout using my bandsaw.
Clean Up & Priming

With all of the pieces cast and the pouring spouts cut off, everything needed just a little bit of clean-up. Anything that was cast from a two part mold had a bit of flashing along the seam that needed to be sanded off.

Every surface got a bit of a buffing with a high grit sanding sponge. This gave the surface a little bit of tooth for the paint to grab on to. Then every piece got hit with a good layer of rattle can primer and was allowed to dry.

Masking, Painting, and Stencils
The first part of the painting process was to lay down the base coat of color. Most of the pieces for this guy either got a black or a white base coat, depending on the dominant color for that piece. Then I did a lot of masking. Especially on the main body piece, there were several areas that got a different color of paint, so they were masked off with tape before the next layer of paint was sprayed on.

Once areas were masked off, however, all that was needed was to apply a couple coats of spray paint to those areas to get the desired effect. For some of the pieces this was done multiple times to paint areas with different colors.

Other parts of the gun had some fairly intricate designs and logos on them, so I needed to make some stencils. This is where a vinyl cutter comes in really handy. I drew up the designs in Inkscape and cut them out in a low tac masking vinyl. The same thing can be done with masking tape, an X-Acto knife, and a steady hand.

These stencils were laid down on their respective pieces and then sprayed with some clear spray paint before spraying or brushing in the colored paint. This clear paint will clog any gaps between the stencil and the piece where color might sneak through. Once the clear paint was dry, I sprayed or brushed on my decal paint. When that layer dried, I removed the stencil to show a super crisp looking decal below. When I was happy with all of the paint, everything was shot with a good layer of matte clear spray paint to seal in our hard work.
Assembly
This kit has 34 pieces. That’s a lot of bits and bobs floating around the shop. Once most of the paint was applied and dry, I could finally get down to attaching them all together. Where possible, I put a metal screw or a pin in between two pieces before gluing them together. This would increase the effectiveness of the bond.

For the most part, I used super glue to attach all the resin pieces. If I needed a little bit of time to adjust the pieces, I employed a 5 minute epoxy. This was the case with all 24 of the tubes along the barrel. I wanted to make sure they were all aligned, so the extra cure time on that epoxy really helped.

I knew that hollow tube on the bottom of the gun was going to be a nuisance come shipping time, so I made it removable. A threaded rod was glued into the gun body and then I cut out a round disc from PVC plastic and sunk a t-nut into it. This disc screwed onto the gun body and also fit into that cast tube piece. I glued the disc into the tube, creating a removable part that screwed flush to the gun body.
Weathering
Weathering this gun was a whole lot of fun. Most of it was done with simple acrylic paints in black, brown, burnt sienna, and yellow ochre colors. Since a lot of the gun was white, it really gobbled up a lot of the color. In fact, I spent a lot of time trying to remove my weathering paint, rather than applying it. Most of it was done by cramming a bunch of paint all over a piece and then trying to clean it up with a paper towel.

The tube on the top/rear of the gun is the only piece that looks like it’s made of exposed metal, so of course I wanted to rust the crap out of it. For this one I used real rust in the form of a system from Sculpt Nouveau. I painted on their iron colored metallic paint in areas that I wanted to be rusty. Then, before the paint could dry, I sprayed on their patina solution and waited. A few hours later we had some super legit rust.

The last little bit of grime was a puddle of tinted epoxy dribbled on part of that rusty tube. This epoxy cured solid and shiny, so that it would always look wet and gross.

Finally I did just tiny bit of edge weathering with a silver Sharpie to make it look like some of the edges had worn through the paint to the metal below. I know in the past I have way overdone this effect, so for this gun I dialed it way back and I’m pretty happy with the results.
After one more blast of matte clear primer (taking care to mask that shiny goo) and this gun was completely finished! HURRAY!


Final Thoughts
This was easily my most ambitious project to date. It was extremely challenging and I didn’t give myself much time to complete it. A massive thanks goes out to my wife Brittany who helped out a ton in the matrix molding process and did a lot of the casting and painting of all those obnoxious little bits and pieces. I couldn’t have done it without her!
Thanks to the gang at Tested for giving me the opportunity to share this project with you guys and, of course, thanks to Smooth-On for providing all of the casting and mold making materials. Let’s do this again some time!
Find more of Bill’s work on his Punished Props website and YouTube channel.
Thanks to Smooth-On for providing materials for this build. Subscribe to their YouTube channel here.
7 thoughts on “Building a District 9 Alien Rifle Replica, Part 4”
Leave a Reply
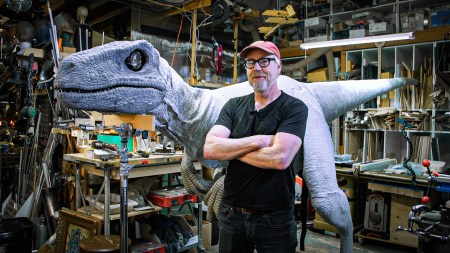
One Day Builds
Adam Savage’s One Day Builds: Life-Size Velocirapt…
Adam embarks on one of his most ambitious builds yet: fulfil…
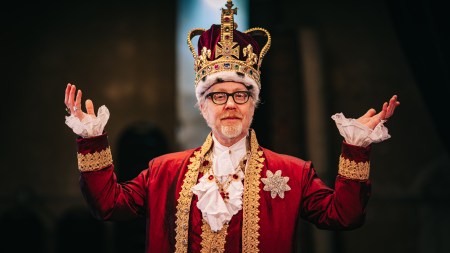
Show And Tell
Adam Savage’s King George Costume!
Adam recently completed a build of the royal St. Edwards cro…
All Eyes On Perserverance – This is Only a Test 58…
We get excited for the Perserverance rover Mars landing happening later today in this week's episode. Jeremy finally watches In and Of Itself, we get hyped for The Last of Us casting, and try to deciper the new Chevy Bolt announcements. Plus, Kishore gets a Pelaton and we wrack our brains around reverse engineering the source code to GTA …
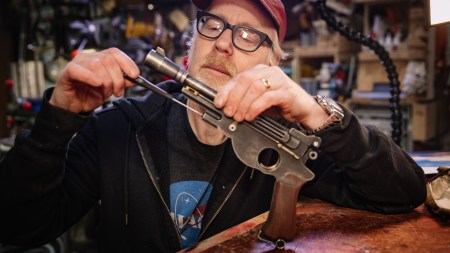
One Day Builds
Mandalorian Blaster Prop Replica Kit Assembly!
Adam and Norm assemble a beautifully machined replica prop k…
House of MCU – This is Only a Test 586 – 2/11/21
The gang gets together to recap their favorite bits from this past weekend's Superb Owl, including the new camera tech used for the broadcast and the best chicken wing recipes. Kishore shares tips for streamlining your streaming services, and Will guests this week to dive into the mind-bending implications of the latest WandaVision episod…
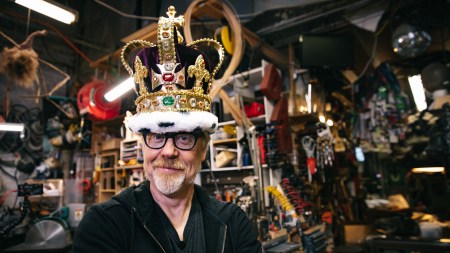
One Day Builds
Adam Savage’s One Day Builds: Royal Crown of Engla…
One of the ways Adam has been getting through lockdown has b…
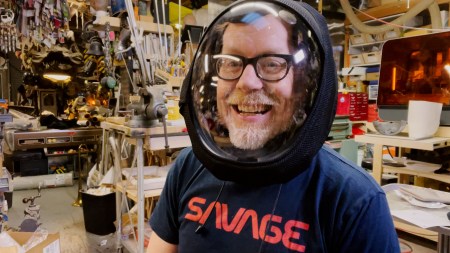
Making
Adam Savage Tests the AIR Active Filtration Helmet…
Adam unboxes and performs a quick test of this novel new hel…
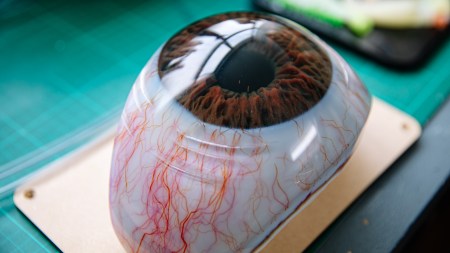
Making
Weta Workshop’s 3D-Printed Giant Eyeballs!
When Adam visited Weta Workshop early last year, he stopped …
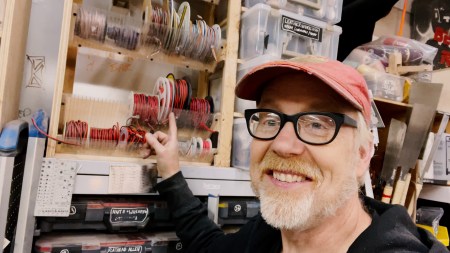
One Day Builds
Adam Savage’s One Day Builds: Wire Storage Solutio…
Adam tackles a shop shelf build that he's been putting off f…

Show And Tell
Mechanical Dragonfly Automata Kit Build and Review
Time for a model kit build! This steampunk-inspired mechanic…
^_^
This gun is an incredible design, and an awesome replication!
That rifle looks amazing Bill!
Thanks! =)
Really great work and unbelievable attention to detail.
well done on the project. For allot of firsts you must be happy that no major disasters happened.
I do have a few questions for you;
In the giant matrix mold did you add the external resin pour hole in post? in that same process did you add any air-escape sprues/trenches?
Also I assume the resin is a polyurethane base, and I was wondering about specific glues to use.
In my younger years when gluing styrene, it would part melt the model and great a ‘welded’ bond. I’m finding when dealing with resin that doesn’t happen. This means two parts that meet need super-acurate surfaces so they line up. Welding on the other hand allows for flexibility.
Are there any glues for 2 part resin that will melt the surface, or do I need to revise my molding/casting process?
Thanks! I didn’t need any air vents or sprues. I did add a large, silicone plug for the back end pouring area, technically making it a 4 part mold. It also gives me the option to plug it and slush cast the rifle body.
Most of the gluing for this piece was done with super glue, unless I needed some working time. In those cases I used a 5 minute epoxy. I don’t know that there are any glues that actually melt urethane, but I’ve never needed that. If I’m worried about a part being too weak of a bond, I use metal pins along with the super glue or epoxy.
Thanks for the reply, and again for the series. Your tips and guide on mold making has helped me see that by spending more time on a complex mold saves time on cleaning up and assembling casts.
Also many thanks on showing the technique on casting the rifle body. I was at Weta last month where they have the same prop on show. The guide tried to explain pouring resin in both halves of the mold and placing one onto another. This video shows the technique wonderfully.