PREMIUM – Model Behavior: Making Custom Wood Blaster Grips!
Bill’s back for another Fusion 360 tutorial in our shop! This week, we step up to modeling more complex shapes with the making of wooden grips for the Dave Goldberg snub-nosed Blade Runner blaster prop. And these grips are going to be milled in a CNC machine instead of 3D-printed!
16 thoughts on “PREMIUM – Model Behavior: Making Custom Wood Blaster Grips!”
Leave a Reply
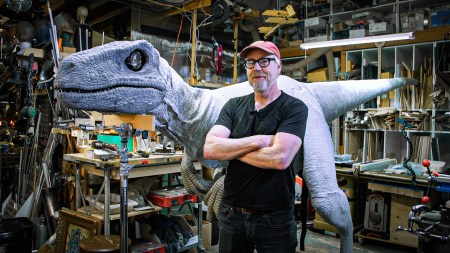
One Day Builds
Adam Savage’s One Day Builds: Life-Size Velocirapt…
Adam embarks on one of his most ambitious builds yet: fulfil…
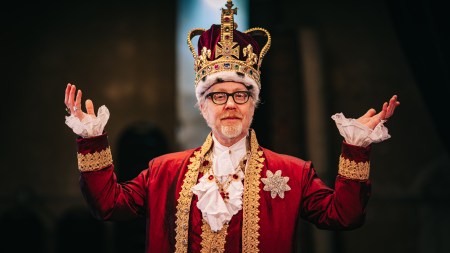
Show And Tell
Adam Savage’s King George Costume!
Adam recently completed a build of the royal St. Edwards cro…
All Eyes On Perserverance – This is Only a Test 58…
We get excited for the Perserverance rover Mars landing happening later today in this week's episode. Jeremy finally watches In and Of Itself, we get hyped for The Last of Us casting, and try to deciper the new Chevy Bolt announcements. Plus, Kishore gets a Pelaton and we wrack our brains around reverse engineering the source code to GTA …

Making
Adam Savage in Real Time: God of War Leviathan Axe…
Viewers often ask to see Adam working in real-time, so this …
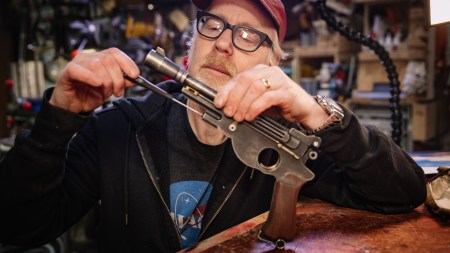
One Day Builds
Mandalorian Blaster Prop Replica Kit Assembly!
Adam and Norm assemble a beautifully machined replica prop k…
House of MCU – This is Only a Test 586 – 2/11/21
The gang gets together to recap their favorite bits from this past weekend's Superb Owl, including the new camera tech used for the broadcast and the best chicken wing recipes. Kishore shares tips for streamlining your streaming services, and Will guests this week to dive into the mind-bending implications of the latest WandaVision episod…
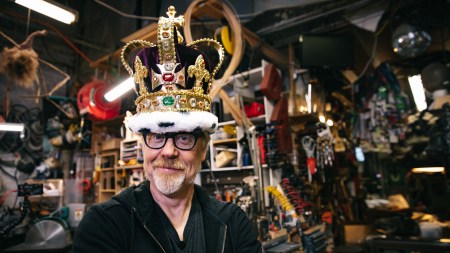
One Day Builds
Adam Savage’s One Day Builds: Royal Crown of Engla…
One of the ways Adam has been getting through lockdown has b…
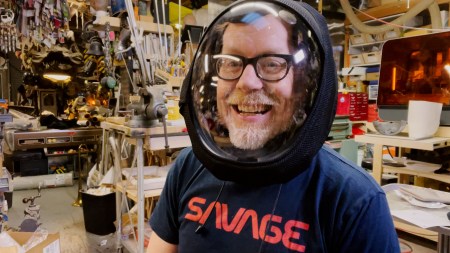
Making
Adam Savage Tests the AIR Active Filtration Helmet…
Adam unboxes and performs a quick test of this novel new hel…
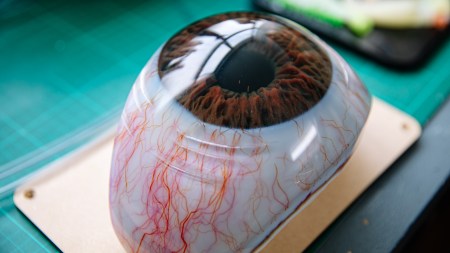
Making
Weta Workshop’s 3D-Printed Giant Eyeballs!
When Adam visited Weta Workshop early last year, he stopped …
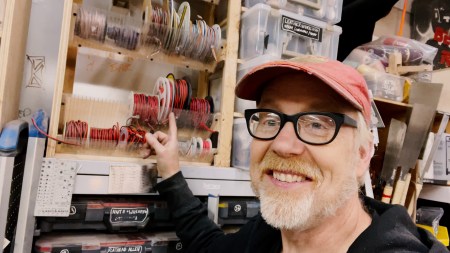
One Day Builds
Adam Savage’s One Day Builds: Wire Storage Solutio…
Adam tackles a shop shelf build that he's been putting off f…
Bill – Great work on modeling grips to fit my snub nose blaster! I really like your very informative step by step description of how to work in Fusion.
Having CNC’d a few sets of wooden grips for the blaster myself I have a suggestion. Do all of the surface machining first with the exception of the checkering. Cut out the grips from the block and do all of the finish work including sanding, oil/varnish, wax, etc. Then go back and add the checkering, followed by some more oil. This way you don’t have to worry about rounding off any of the checkering when sanding. You can make a jig using the two mounting holes to position the sanded grips back in the CNC.
While sanding up to the checkering isn’t too difficult, this method allowed me to use a power buffing wheel and rouge to get a glass-like surface on the wood.
Looking forward to more tutorials!
Edits though, “Nope, we don’t need a jump-cut.”
Thanks. Nice to see you use a CNC mill.
Norm asked whether the 2D contour cut would run on the inside or outside of the sketch line. I don’t think Bill quite answered this question, at least not on camera. This is selectable in F360. When you select the chain (the sketch line) under the GEOMETRY tab a red arrow appears on the thick blue line that indicates the chain. Clicking again on the chain (the blue line) will reverse the direction of this arrow. If the arrow is pointed one way (clockwise, for instance, from the top view) around the chain, the endmill will cut along the OUTSIDE of the chain. Pointed the other way and it will cut INSIDE the chain. It is really easy to reverse this as you tweak and adjust the tool paths for a complex part, or multiple parts cut from a single piece of stock. Getting it wrong means your part will be undersized/oversized by the diameter of the cutter.
Its good practice to zoom in on the tool paths, to make sure that they are all running on the correct (intended) side of the line in addition to simulating the operation, before posting the g-code.
Norm asserted that the CAM operations have “no knowledge of the past. “Rest machining” kind of takes care of this — so that you don’t spend a lot of time cutting air.
Oh, and “vertex” is the singular of “vertices” (smile)
Beautiful work!!! Love these videos! Keep them coming!
Wow I’m blown away by this video, wishing I had a workshop
I’m wondering why Bill didn’t simply track the contour, than exdrude and bevel the shape.
All in all it’s a good idea to show the whole process. Next step: Tested makers on Twitch for live creations! 🙂
Awesome video, I wish I had a CNC machine! Just one little niggle: the singular of vertices is vertex not vertice… 😉
The Z-axis orientation is a historic carry-over from 2D drawings. The X-axis would have been from left to right an Y up and down the page, this being the ‘front’ view. A theoretical Z-axis would then have been pointing out of the page and towards the draughtsperson. When 3D cad came along, this convention carried over. For anyone coming new to 3D CAD, having the Z-axis vertical makes more sense.
Having said that, the coordinate system can be set in the CAM environment and it’s worth noting that Z is by convention parallel with the spindle axis, so on a lathe, the Z-axis is horizontal and the cross-slide is the X-axis.
Arts Thanks Dave! You’re a wizard. =D
Fantastic info, thanks for sharing!
That is SUPER interesting! =D
There’s also potentially an easier/better way of doing the chequering. Instead of using sketch geometry in the CAD, use the parallel toolpath in the CAM. You can set the path angle and stepover. A second parallel op at the complementary angle and you’re sorted.
Bill- So great to see another maker using Fusion. I second the “rest machining” option. Thank you for this.
Norm- As a trained gunsmith it behooves me to correct your terminology: the triangles or diamonds cut into gunstocks or pistol grips is called checkering. Cutting them with a CNC and then chasing with a checkering for or checkering tool has saved me countless hours and headaches. I’m so glad you showed this.
Keep it up, I’m looking forward to seeing more.
Love these process steps and thinking through the machining to inform your design. Always best to model with your later steps in mind. PressTurbo is correct in his assertion about checkering. You guys kept saying “knurling”, but knurling is pressing the pattern into your material with a knurl by deforming, not removing any material (usually done on a lathe and usually with metal). Since you guys are milling out material to create a pattern you are checkering. It may seem like picking knits but with a video this technically accurate on everything else it seemed out of place. Great job guys.
Sweet!!!!!! More Fusion 360 🙂
Thanks so much for these tutorials!!! I can finally make my way around fusion without getting completely frustrated. Please keep them coming!!